Direct cardboard marking
Cardboard boxes and cartons made of paper and cardboard are ideal as primary and secondary packaging for transporting and storing products safely and reliably along the entire transport chain to the customer.

Above all, however, primary and secondary packaging have to be reliably marked with a range of important information. Important information that supports logistics (movement of goods, traceability) and consumer protection. These are
- Description of goods
- Article number
- Batch number
- Best before date
- Storage instructions
- Barcodes
- Matrix codes
- Branding
This information can be applied to the packaging in various ways:
- pre-printed cardboard boxes
- Labels
- digital direct printing
The trend in the industry is towards a greater variety of products with individually smaller quantities and order-related production.

Marking with digital direct printing
Sustainable, flexible and cost-efficient solution
Digital direct printing is cost-efficient, flexible and sustainable - especially in comparison to pre-printed cardboard packaging and labels - and thus meets the spirit of the times in the industry. The printers for direct cardboard marking are small, compact and can be easily integrated into the production line, even where space is limited.
Static and variable data can be permanently applied contact-free with direct printing. Combinations of static print content such as logos or symbols and variable print content such as date, time, counter or shift code are just as possible as purely variable or static data. This allows the greatest possible scope for individualizing the print content. A printing system with flexible print head alignment allows even more flexibility.
While the space for the information to be conveyed is limited with labels, digital direct printing allows large and high-resolution print images to be created with all relevant information. Barcodes and 2D Codes can also be printed reliably and with the required edge sharpness and contrast. Several print heads can be used in cascade to increase the print area.
Digital printing systems are generally low-maintenance and require nothing more than new ink on a regular basis. This eliminates the need to stock pre-printed cardboard packaging. The same applies to pre-printed labels. Material management is simplified by the low-maintenance printing systems. This is because changeover times, which would otherwise occur during operation and cause machine downtime, can be reduced to a minimum.

What are the advantages of direct cardboard marking?
Inkjet instead of labels
- Only one printing system required, which can be integrated into production thanks to its compact design
- No expenditure on versatile consumables such as pre-printed cartons or labels and their storage space and administration
- No expensive downtimes due to set-up times when changing products, changing label rolls or changing carton layouts
- Economical ink consumption, low maintenance requirements
- Higher printing speed, lower printing costs per print
- Permanent, and therefore no peeling of the print or poor adhesion
Which coding and marking system is suitable for direct cardboard marking?
REA JET GK 2.0 - REA JET High Resolution Inkjet Printer:
The new generation of high-resolution inkjet printers REA JET GK 2.0 prints freely combinable texts, logos and graphics with variable print data. A horizontal resolution of up to 1,200 dpi ensures print results with high edge definition - and at print heights of up to 100 mm. With their compact design, the devices can be easily integrated into production. They are also fully Industry 4.0-capable.
- High resolution marking up to 100 mm print height
- For paper, cardboard, corrugated cardboard, shipping packaging, paper cores, continuous corrugated cardboard, continuous paper
- Sharp-edged marking on absorbent surfaces
- Cascading of several print heads for large print images
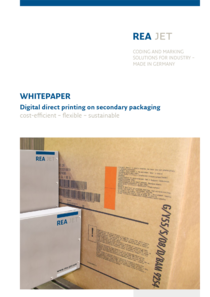