Märkning av säckar för bulkvaror
Säckar eller påsar används alltid som primärförpackning när produkten är i form av pulver, granulat eller bitar. Det kan röra sig om papperssäckar eller plastsäckar. Förutom själva fyllningsprocessen är det viktigt med en tydlig och spårbar märkning av de förpackade varorna.

Kraftig och lämplig för industriell användning
Branscher och produkter
Säckmärkning måste vara snabb och tillförlitlig utan att kompromissa med märkningens utskriftskvalitet. Detta beror på att märkning av säckar med bulkvaror ofta sker under tuffa och ogynnsamma tekniska förhållanden. Höga nivåer av dammföroreningar, temperaturvariationer och vibrationer är snarare regel än undantag. Trots de tuffa miljöförhållandena är det lätt att uppnå kontrastrika och perfekt läsbara tryckresultat. I produktioner med liten dammförorening kan till och med högupplösta utskriftsresultat med till exempel 1D- och 2D-koder produceras.
Bulkvarorna omfattar följande branscher och produkter:
- Byggmaterialindustrin : sand, grus, cement, gips, betongblandning, krossad sten, flis, pulverlackering, keramiskt pulver, granulat, kalk
- Livsmedelsindustri: mjöl, spannmål, socker, salt, stärkelse, kaffe, livsmedelstillsatser, frön, ris, bakråvaror, livsmedelspulver, te, kryddor, malt
- Pappersindustri: stärkelse
- Kemisk industri: pigment, fyllmedel, granulat, gödningsmedel, kemikalier, stärkelse, svavel, natrium, kalcium, talk, pulver, plastpulver
- Djurfoderindustrin: pellets, mineralfoder, djurfoder
Utskriftsavstånd, styrskena, avståndsutjämning
Hur märks säckar med bulkvaror?
I de flesta fall sker märkningen efter att produkten har fyllts i säckarna eller påsarna. Säckarna flyttas på transportband och märkningen appliceras direkt på säckarna ovanifrån eller från sidan. Utmaningen vid märkning av säckar från sidan är att säkerställa en jämn utskriftsyta och rätt avstånd till skrivhuvudet. Detta uppnås genom att produkten styrs korrekt med hjälp av en styrskena. Alternativt kan en avståndsutjämnare användas, som sekvenserar påsens kontur och därmed kompenserar för olika påsstorlekar.
Om märkningen däremot sker innan säckarna eller påsarna fylls, spelar dammföroreningen i allmänhet en underordnad roll. Detta gör det också möjligt att uppnå högupplösta tryckresultat. Information som streckkoder eller Data Matrix-koder kan då enkelt skrivas ut direkt på påsarna. Alternativt kan etiketterna appliceras genom blåsning, sugning eller rullning.
Information som t.ex.
- Bäst före datum
- Produktionsdatum
- Fyllningsdatum
- Batchnummer
- Skiftkoder
- 1D-koder
- 2D-koder
- Viktkoder
- UFI-kod
- Unik identifiering av enheter (UDI)
Lämpliga system för kodning och märkning av bulkvaror
Snabbt, robust, tillförlitligt
Under vilka förhållanden märkningen ska ske, om märkningen ska ske före eller efter fyllningen och vilket utskriftsresultat som ska uppnås - det är de krav som måste definieras för ett system för kodning och märkning. Lämpliga REA Kodnings- och märkningssystem är
REA JET DOD 2.0 - bläckstråleskrivare för stora tecken:
- Används under de svåraste miljöförhållanden
- Robusta, tillförlitliga skrivhuvuden
- Stora utskrivna bilder
- Kan användas oavsett material
- För fyllda och ofyllda säckar eller påsar och stora förpackningar
- Modulär design för kundanpassad konfiguration
- Stort urval av bläck
REA JET HR - Högupplösta bläckstråleskrivare:
- Högupplöst märkning för optimal läsbarhet och kodkvalitet
- Kan användas oavsett material
- För fyllda och ofyllda säckar eller påsar
- Stort urval av bläck
- Underhållsfri
- Ett nytt skrivhuvud vid varje patronbyte
- Bulksystem för låga bläckkostnader med hög genomströmning
REA JET GK 2.0 - Högupplösta bläckstråleskrivare:
- Högupplöst märkning
- Lämplig för ofyllda, tomma påsar
- Märkning med skarpa kanter på absorberande ytor
- Kaskaderade skrivhuvuden för stora utskriftsbilder
REA LABEL - Teknologi för etikettering:
- Etikettering av plast- och papperspåsar
- Lämplig för ofyllda och fyllda påsar
- Modulär design för kundanpassning
- Ger stort utrymme för kundanpassad och applikationsspecifik systemdesign
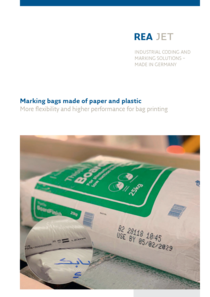